PREMISES NAME
Sushi Farm | Tel: (778) 985-6189
Fax: |
PREMISES ADDRESS
780 Princess St
New Westminster, BC V3M 5X5 | INSPECTION DATE
September 6, 2017 | TIME SPENT
1 hour |
OPERATOR (Person in Charge)
Hua Wen Liang | NEXT INSPECTION DATE
September 13, 2017 |
INSPECTION TYPE
Routine |
ACTION TAKEN |  | FOOD SAFETY & SANITATION |
ADMINISTRATIVE
Information Provided | ENFORCEMENT
Require Corrections |
 | Comply | In Use |
Food Safety Training [s. 10] | Yes |  |
Food Safety Plan [s. 23] | Yes | No |
Sanitation Plan [s. 24] | Yes | No |
|
HAZARD RATING FOR YOUR FACILITY: Moderate (16-29) Total Score = 22 |
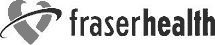 | TRANS FAT REGULATION ENFORCEMENT REFERENCE
Health Protection
Report #: AKWN-AQXTE3 |
COMPLIANCE REQUIREMENTS FOR FOOD PREPARED, SERVED OR OFFERED FOR SALE LOCATED ON THE PREMISES OF A BC FOOD SERVICE ESTABLISHMENT: |
Time Spent: 0.17 hour Specific comments: Reviewed product information for canola oil. |
Food exempt from the regulation includes:
- Pre-packaged food with a Nutrition Facts table sold directly to the consumer without alteration
- Food with the sole source(s) as naturally occurring trans fat (i.e. beef, sheep, lamb, bison and dairy products)
- Employee lunches not purchased from the food service establishment
|