PREMISES NAME
Pink Lotus Cafe | Tel: (604) 543-0515
Fax: |
PREMISES ADDRESS
104 - 16016 Fraser Hwy
Surrey, BC V4N 0G3 | INSPECTION DATE
January 18, 2018 | TIME SPENT
1.25 hours |
OPERATOR (Person in Charge)
Meng Ong | NEXT INSPECTION DATE
January 31, 2018 |
INSPECTION TYPE
Routine |
ACTION TAKEN |  | FOOD SAFETY & SANITATION |
ADMINISTRATIVE
Information Provided | ENFORCEMENT
Require Corrections |
 | Comply | In Use |
Food Safety Training [s. 10] | Yes |  |
Food Safety Plan [s. 23] | Yes | No |
Sanitation Plan [s. 24] | Yes | No |
|
HAZARD RATING FOR YOUR FACILITY: High (≥30) Total Score = 43 |
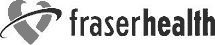 | TRANS FAT REGULATION ENFORCEMENT REFERENCE
Health Protection
Report #: JCHW-AV5V72 |
COMPLIANCE REQUIREMENTS FOR FOOD PREPARED, SERVED OR OFFERED FOR SALE LOCATED ON THE PREMISES OF A BC FOOD SERVICE ESTABLISHMENT: |
Time Spent: 0.08 hour Specific comments: Margarine: 0g trans fat / 8g total fat = less than 2% trans fat
Oil: no trans fat
Other food items: meet trans fat requirements. |
Food exempt from the regulation includes:
- Pre-packaged food with a Nutrition Facts table sold directly to the consumer without alteration
- Food with the sole source(s) as naturally occurring trans fat (i.e. beef, sheep, lamb, bison and dairy products)
- Employee lunches not purchased from the food service establishment
|