PREMISES NAME
Kelly's Pub | Tel: (604) 543-4032
Fax: |
PREMISES ADDRESS
112 - 7218 King George Blvd
Surrey, BC V3W 5A5 | INSPECTION DATE
January 28, 2019 | TIME SPENT
1 hour |
OPERATOR (Person in Charge)
Jasmine Saini | NEXT INSPECTION DATE
6 Months |
INSPECTION TYPE
Routine |
ACTION TAKEN |  | FOOD SAFETY & SANITATION |
ADMINISTRATIVE
Information Provided | ENFORCEMENT
Require Corrections |
 | Comply | In Use |
Food Safety Training [s. 10] | No |  |
Food Safety Plan [s. 23] | Yes | Yes |
Sanitation Plan [s. 24] | Yes | No |
|
HAZARD RATING FOR YOUR FACILITY: Low (≤15) Total Score = 13 |
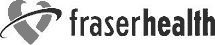 | TRANS FAT REGULATION ENFORCEMENT REFERENCE
Health Protection
Report #: JCHW-B8URUP |
COMPLIANCE REQUIREMENTS FOR FOOD PREPARED, SERVED OR OFFERED FOR SALE LOCATED ON THE PREMISES OF A BC FOOD SERVICE ESTABLISHMENT: |
Time Spent: 0.08 hour Specific comments: Margarine had 0.4g trans fat / 80g total fat = less than 2% trans fat
Oil is trans fat free
Other foods meet the trans fat requirements |
Food exempt from the regulation includes:
- Pre-packaged food with a Nutrition Facts table sold directly to the consumer without alteration
- Food with the sole source(s) as naturally occurring trans fat (i.e. beef, sheep, lamb, bison and dairy products)
- Employee lunches not purchased from the food service establishment
|